Acoustic or electric, the guitar is a very complex instrument to make. They are very beautiful, tactile objects that can trace their roots back thousands of years.
Before Brian May, Jimi Hendrix, Prince and Slash, there were stringed instruments. Known as chordophones, they were played in ancient cultures around 3,000 to 4,000 years ago, and varieties of similar stringed instruments were common among ancient and early mediaeval cultures. By the sixteenth century, there were two main varieties of chordophone, a small, rather quiet rounded instrument called a lute, and the vihuela, which was much like the acoustic guitars we know today.
Fast-forward to the nineteenth century and the classical guitar you can buy today was perfected by legendary Spanish instrument maker Antonio Torres Jurado. His pioneering work influenced how guitars were manufactured for decades to come, essentially defining what we know today as the modern acoustic guitar.
The electric guitar made its first appearance in the early 1930s, and these modern guitars have become as famous as the great rockers who played them – including Hendrix’s Monterey Stratocaster, Kurt Cobain’s Fender Jag-Stang, Brian May’s Red Special and Jimmy Page’s double-necked Gibson EDS-1275 (the guitar that took Led Zeppelin on a Stairway to Heaven).
Here, we’ll give you the lowdown on how guitars are built.
Craftsmanship Personified - The Acoustic Guitar
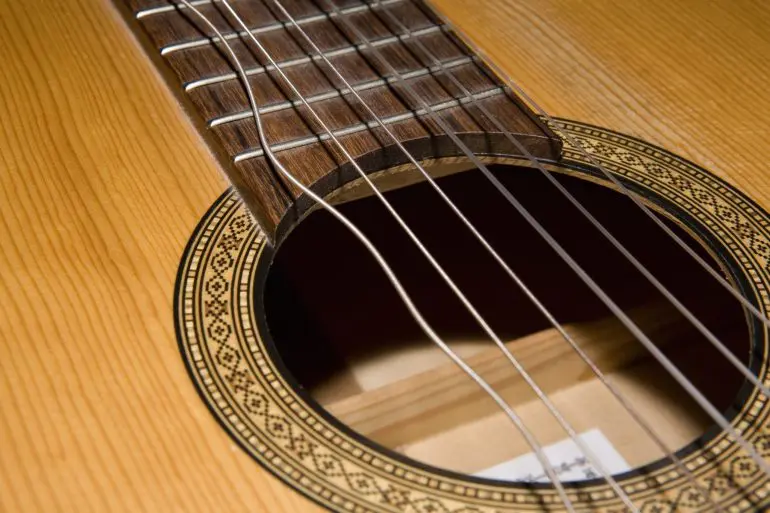
A guitar with a broken string (Photo: Caspar Benson via Getty Images)
How are acoustic guitars made? While each individual manufacturer will have their own trade secrets about how guitars are built, generally speaking most will follow the same core process:
The Body
When it comes to manufacturing guitars, the materials are as important as the process. The sides and back of the best acoustic guitars are made from Brazilian or East Indian rosewood, due to its exceptional sound quality. The top is usually made of spruce, the neck from maple or mahogany and the fretboard from ebony.
Building the body of the guitar is a process that takes skill, years of experience and a keen eye for detail. The top and bottom of the guitar are cut into their classic and distinctive shape from the same piece of wood so they are symmetrical, in a process known as bookmatching.
The wood for the sides of the guitar is either steamed or submerged in warm water to make it soft and pliable, and then each side is gently moulded to fit the figure-of-eight shape of an acoustic guitar. Once the craftsman is happy with the shape, the top and bottom are fixed to the sides with a very strong wood adhesive and the body is complete.
The Details
The neck is carved from a single piece of wood reinforced with a wooden rod. This is sanded until smooth, and then the fretboard is attached. It’s at this point the steel frets are attached into pre-cut grooves. The fret is one of the most beautiful pieces of the guitar and some are inlaid with stunning hand-carved detail.
The neck is fixed to the body, and the saddle and bridge (the raised piece of plastic or synthetic bone that attaches the strings to the body) are attached. At the top of the neck, the nut is fixed to hold the strings in place. The tuning pegs are added, along with any maker’s logos. Aside from quality control, and fine tuning, at this point the guitar is essentially complete.
The Electric Guitar - The 20th Century Soundtrack
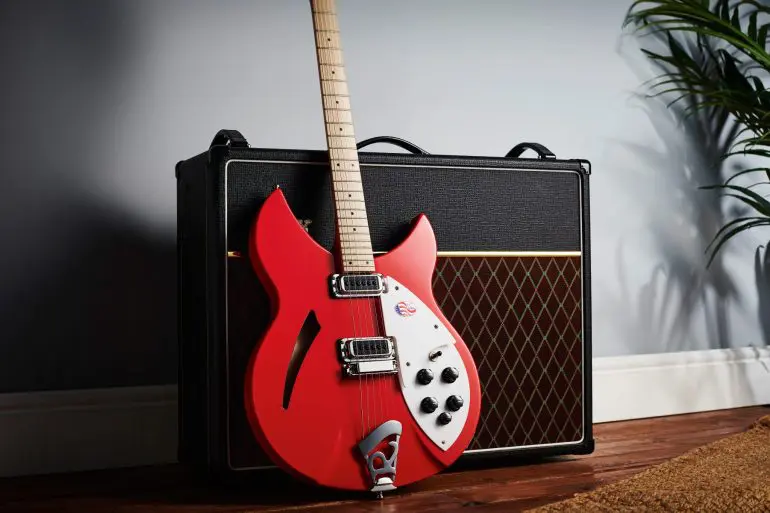
A Rickenbacker 330 Limited Edition electric guitar with a Pillar Box Red finish (Photo: Guitarist Magazine via Getty Images)
How are electric guitars made? Like the acoustic or classical guitar, it is a very precise, elaborate process that can’t be rushed.
The Body
When considering how electric guitars are built, the debate rages on and on about the best wood to use. Generally speaking maple, ash and alder are favoured by purists, as they offer the best tonality. Whichever wood is used, it’s left to dry in order to reduce the moisture content and crystallise resin in the wood as much as possible. Dryer wood is more stable.
Each manufacturer will use a combination of different woods to make the component parts of their guitars, for example the Fender Strartocaster has an alder body, a maple neck and a maple or pau ferro fretboard. The Gibson Les Paul Standard 60s has a mahogany body and neck, and a rosewood fretboard.
The body and the neck are fixed together in one of three ways. The neck is inserted into the body and glued into place, the neck is bolted to the body, or the neck and body are one single piece of wood. The graceful curve on the underside of the neck is then hand-planed by a master craftsman, who will often make his or her planes by hand to achieve the perfect finish.
The Carving and the Coating
Next, the spaces for the electric circuitry are carved out of the back of the guitar’s body. For mass-produced guitars this is done by machine, but for bespoke pieces it is done by hand. Whichever method is used it must be millimetre perfect.
The coating is another equally precise and time-consuming process when discussing how are electric guitars made. As most hardwoods have a relatively open grain, tiny pores can appear in the body of the guitar which can dramatically affect its sound. Therefore, these tiny holes – some barely visible to the naked eye – must be closed. This is done with a substance known as a grain filler, a clear, water-based paste rubbed over the surface of the guitar which seeps into the small holes and closes them.
A spray gun is then used to apply an undercoat, the desired paint colour and finally a polyurethane resin, which gives the guitar a beautiful shine and protects the wood. It is even said that the sound of the finished guitar can depend on how the coatings are applied.
The Assembly
This is perhaps the most important part of how guitars are manufactured. The electric wiring and circuit board are fixed into the body, the strings are attached, and the bridge and pickups – the elements that convert the string vibrations into electricity to be amplified – are all fixed into place. The nuts, which hold the strings in place, are then attached, as is the headstock where the tuning devices sit. The headstock is usually where the manufacturer’s logo is placed.
As with the final stages of the assembly of acoustic guitars, the electric guitar is tested and fine tuned before being packed up and shipped out.