Red, white or pink, cricket balls have been used since the birth of the game – sometime around the early sixteenth century.
The origin of the word ‘cricket’ has been lost to history, though it may have been derived from the Old English word ‘cryce’ which meant a wooden crutch or staff, or the French word ‘criquet’ which described a type of stick or club.
In the hundreds of years the game has been played, cricket balls have barely changed, though the way they’re made has. Here, you’ll find the answer to the question ‘how do you make a cricket ball.’
From Cork to Caught - How Cricket Balls are Manufactured
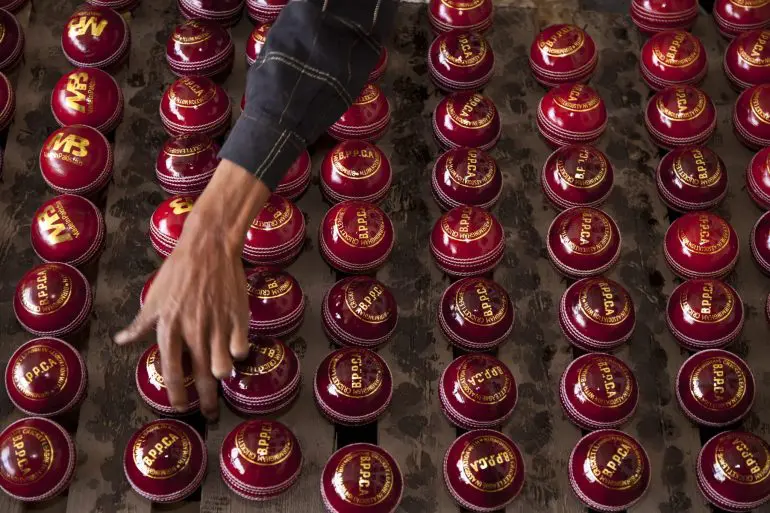
Polishing finished Cricket balls (Photo: Christopher Pillitz via Getty Images)
There are three major cricket ball companies, Dukes in the UK, SG in India and Kookaburra in Australia. Like all good brands, they tend to keep their exact manufacturing processes closely guarded secrets.
According to Law 4.1 of The Laws of Cricket, a new ball must weigh between 155.9g and 163g and the circumference must be between 22.4cm and 22.9cm. With such strict regulations in place, the detail and expertise required in the manufacture of cricket balls remains key.
While everyone would like the answer to ’how do they produce cricket balls’, the makers play their cards close to their chests. Despite this however, the broader processes for manufacturing a cricket ball remain very similar regardless of the manufacturer.
Stage 1 – The Inner Core
The innermost core of a cricket ball is made from cork, often from the Portuguese Cork Oak tree. It is delivered to the manufacturer in sheets which are ground down in a giant hopper and, at the push of a button, the exact amount required is delivered into a mould. Out comes a small round compressed ball of cork roughly the same size as a ping-pong ball.
Stage 2 – The Outer Core
The inner core is then sandwiched between two further slices of cork (on occasion, leather) which are pressed and then glued around the inner cork core. This gives the cricket ball its density and rough shape.
Stage 3 – The Yarn
Once the glue on the outer core is dry, the process of how cricket balls are manufactured really starts to take shape. Each core is then placed in a clamp and wound very tightly with at least five layers of worsted yarn – effectively medium-thickness string which is stronger, smoother and finer than wool with no elasticity. This gives the cricket ball an even bounce and forms the wrapper around the core.
Stage 4 – The Outer Casing
The leather used to cover cricket balls is of the finest quality and comes from cows (in very rare cases buffalo or ox). It is delivered in huge sheets and dyed what is known as ‘test match red’ and then the material is cut to shape. Some manufacturers use two halves and some use four quarters.
The sections of leather are stitched together and put into a mould where they are pressed into perfect hemispheres. Each half-ball is double-stitched by machine to add structural integrity to the ball and then the two halves are hand-stitched together by expert craftsmen using the finest linen thread. This is a process that has stayed almost exactly the same for well over a century.
There are some manufacturers who will stitch the entire ball by hand. The men and women who perfect this craft are often second- and third-generation artisans, who pass their skills down the family line. They know how cricket balls are manufactured because they’ve been doing it for years.
Stage 5 – The Finish
How do you make a cricket ball? Well, we’ve almost answered the question but there are a few more processes to go through before it ends up in the bowler’s hands.
After the balls have been stitched, they are sprayed with a nitrocellulose lacquer that adds strength to the leather and makes it shine.
Lastly, the manufacturer’s name is stamped or pressed onto the ball and they are quality controlled for weight, circumference, bounceability, and to ensure they are perfectly spherical.
Colourful Cricket
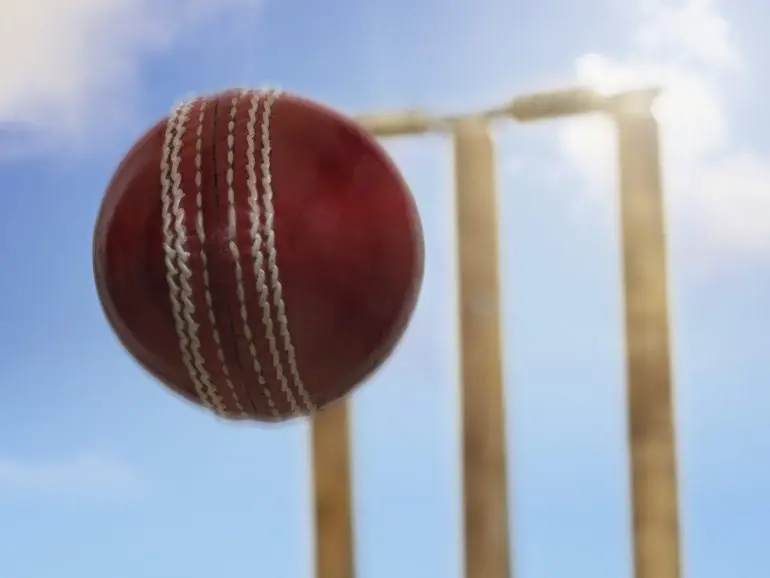
Cricket ball flying towards stumps (Photo: John Rensten via Getty Images)
In recent years white and pink cricket balls have been introduced.
Red balls are used for international test matches as well and first-class county cricket. White balls were introduced when one-day matches and limited-overs matches started to play under floodlights.They are far more visible in twilight and when it’s fully dark.
Pink balls are a halfway point between the two. It’s almost impossible to use white balls in test matches, because they deteriorate so quickly, and it’s very hard to see red balls at night. Therefore, the pink ball was introduced to solve both issues.
How do you make a cricket ball white or pink? Exactly the same way you make red ones, the only difference is the colour of the leather.