Today’s contact lenses have evolved dramatically from the ones invented by ophthalmologist Adolf Fick in 1888.
Fick’s heavy brown glass version covered not just the cornea, but the majority of the wearer’s eye, and required “fitting” by way of making a mould of the user’s eyes. In 1971, Bausch & Lomb released the first soft lenses, which were an immediate hit, selling 100,000 units in their first year alone.
Today, the number of worldwide contact lens users is estimated at a staggering 140 million, and rising at a rate of 4% per year. Despite this, most wearers know little about how those little concave discs are created.
So, how are contact lenses made? And how are coloured contacts made? Are there different answers to “how are soft contact lenses made” versus rigid ones? Let’s find out.
What are Contact Lenses?
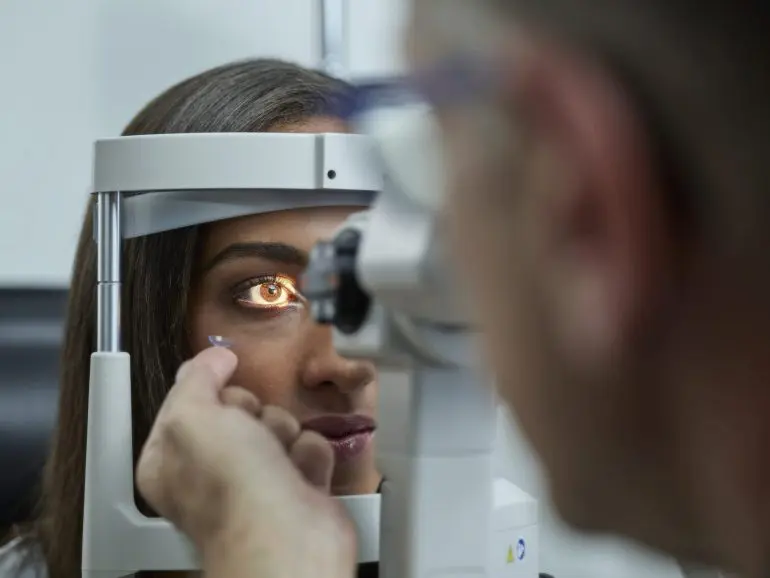
Optometrist examining young woman's eye, contact lens on index finger (Photo: Westend61 via Getty Images)
Before going into the specific steps of making contacts, it’s worth understanding the types of lenses on offer and how they work.
There are myriad varieties of lenses. Daily soft lenses are among the most popular, but weekly and monthly as well as rigid versions are available. There are also ongoing developments such as night lenses, worn while sleeping then taken out and providing all day perfect vision. Some can even be worn continuously for different periods. Most contact lenses are functional, used to correct sight. Others are cosmetic, like coloured contact lenses. There are even therapeutic lenses to protect injured eyes.
Just like glasses, prescription contact lenses refract and focus light to bring vision into focus. The difference is in the “contact”. These ocular prosthetic devices sit directly on the surface of the eye, sticking to or floating on the tear film layer atop the cornea.
So just how are contact lenses made?
How are Contact Lenses Made? Materials
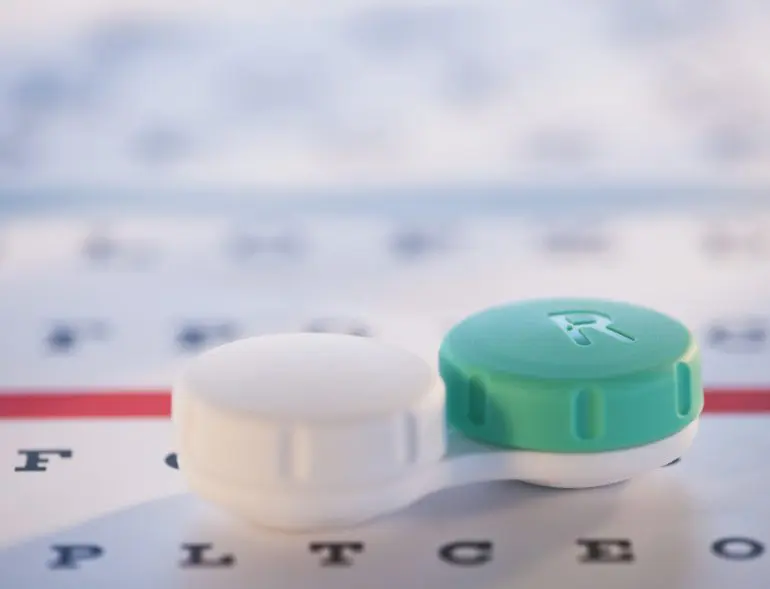
Contact lens case (Photo: Daniel Grill via Getty Images)
While materials may vary from one manufacturer to another – and depending on function – contact lenses are primarily made of plastic polymers, sometimes mixed with monomers. Rigid lenses are usually made of oxygen-permeable plastic polymers incorporating silicon and fluorine. They used to be known as hard lenses, although now this term is used to refer to the older, non-oxygen-permeable kind.
Meanwhile, soft contacts are generally made of a hydrogel. Hydrogels are plastic polymers with hydrophilic qualities, which means they are good at absorbing water, becoming soft and flexible while maintaining their optical properties. Some lenses are made using silicone hydrogels, which allow more oxygen permeability, but are not as wet as pure hydrogels.
The forming of contact lenses involves shaping these plastics into specified curvatures. Different curvatures equate to different prescriptions.
How are Contact Lenses Manufactured?
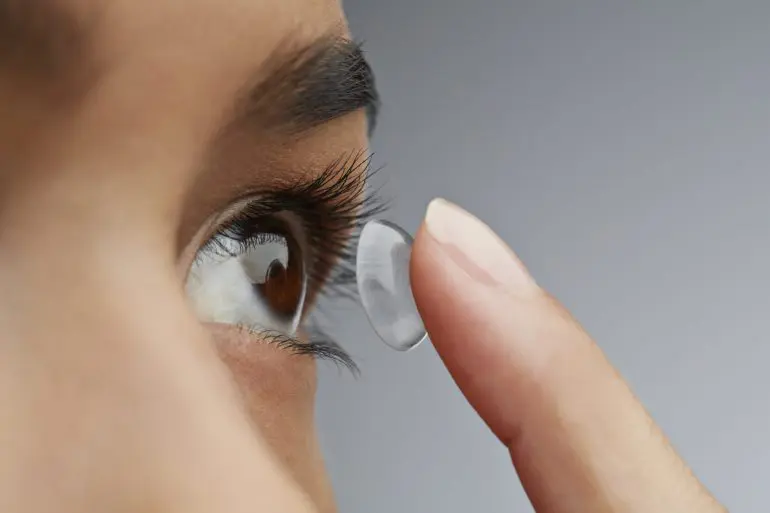
Close-up of woman putting in contact lens (Photo: Klaus Vedfelt via Getty Images)
With such high demand for contacts worldwide, it’s no surprise that they are mass produced. So, how are contact lenses manufactured?
The manufacturing process for contact lenses depends on whether the lenses are soft contacts, rigid gas permeable contacts or hybrid lenses. Most soft contact lenses are mass-produced in a highly automated process that allows for computer-controlled precision and consistency. Rigid lenses on the other hand are custom-made to exact specifications for the individual wearer.
How are Soft Contact Lenses Made?
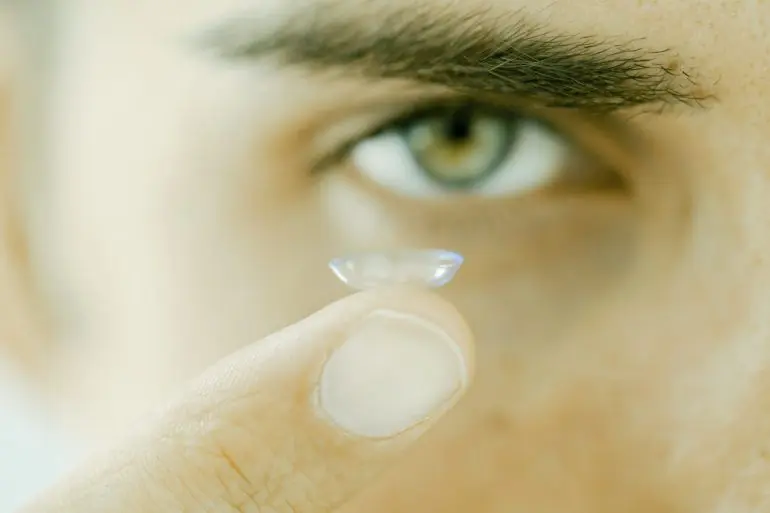
A soft contact lens (Photo: caracterdesign via Getty Images)
The two main manufacturing processes for soft lenses are lathe cutting and injection moulding.
Injection Moulding
As the name suggests, this method starts with injecting molten plastic into a mould under pressure. The mould is made in two parts – a male and female – and curved differently for different prescription strengths. The lens is shaped between the two mould parts. In the past, this has required finishing on a lathe, but more advanced and precise moulding technology has made this unnecessary.
Once shaped, the lenses are cured in special ovens. They are then transferred into their packaging and hydrated in water to make them soft. Contact lens solution is dispensed into each contact lens blister which is then covered with the foil lid by way of heat sealing. The packaged lenses are then heated at over 100 degrees Celsius to sterilise them before a sample from each batch is tested for quality purposes. Faulty batches can be removed, while the rest can proceed to being stamped with their power and manufacturing details.
Lathe Method
The first step in this process is to produce a blank. The blank is a dry plastic polymer circle that has either been stamped from a sheet or cut from a plastic rod and is slightly bigger than the final lens. Using molten wax, the blank is mounted on a steel button, which spins at a high speed of around 6000 rotations per minute. As it does so, an industrial diamond or laser cutter attached to the lathe begins the process of producing the curves of the lens. This involves making cuts, all of which are digitally measured for maximum precision.
Next comes polishing. The button and blank are transferred to a lapping machine for this process. The lapper is a disc that matches the curves of the blank and is covered in an abrasive material. As both the lapper and blank spin in opposite directions and in various formations, the blank is polished. Both the cutting and polishing processes are carried out first on the concave inner surface and repeated on the lens’ convex outer surface. After the front and rear surfaces are finalised, the lens is removed from the lathe and hydrated to make it softer. Quality assurance testing is performed on the finished lenses.
A note about Rigid Lenses
Rigid lenses are made using the lathe method. However, there is a much higher degree of customisation to ensure the perfect fit. Factories that produce rigid lenses place a big emphasis on monitoring the ownership of each set of lenses. Rigid lenses tend to arrive dry, with the prescribing doctor soaking them in solution before dispensing them to the individual client.
Spin Casting
There is also the older “spin cast” method in which different liquids are spun in a mould, the centrifugal force producing the inner curve and the mould the outer curve.
The Whole Picture
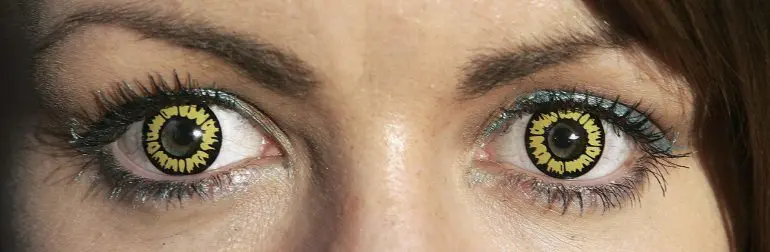
'Wolf Eyes' coloured contact lenses (Photo: Peter Macdiarmid via Getty Images)
And that’s the whole picture. Hopefully this has provided a clear and focused guide to the world of contact lenses, answering a number of questions, including:
- How are contact lenses made?
- How are soft contact lenses made and how does it differ from rigid ones?
- How are colored contacts made?
- How are contact lenses manufactured?