Silicon and silicone are both versatile materials that perform vital roles in modern life. They are both durable and heat-resistant, which makes them ideal for use in a wide range of applications. In fact, they’re vital components in countless aspects of modern life. Yet, thanks to their similar spelling, the two are often confused.
So what is the difference between silicon and silicone? Silicon is a naturally occurring element that is found in sand and quartz. It’s represented by the symbol Si and the atomic number 14. It is a hard and brittle crystalline solid with a blue-grey metallic lustre, and is a tetravalent metalloid and semiconductor. Its oxide form, silicon dioxide, is the second most abundant compound in the Earth’s crust, after water.
Silicone, on the other hand, is a synthetic polymer made up of siloxane, which is a chain of alternating silicon and oxygen atoms. Yes, you read that right. Silicone contains silicon. So, we’ll be taking this in two parts. First, we’ll answer, how is silicon made from sand? And second, how is silicone made from silicon?
Silicon: Millions of Years in the Making
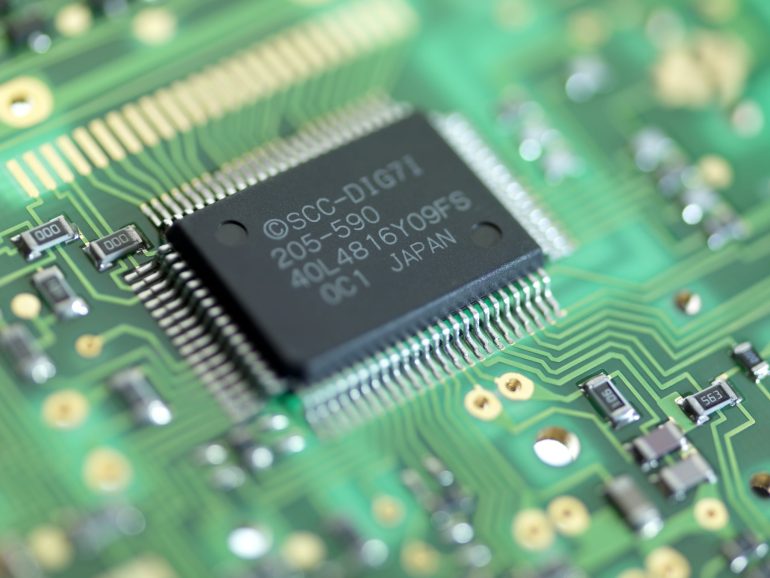
Microprocessor chip in circuit board containing silicon (Photo: Science Photo Library - TEK IMAGE. via Getty Images)
Silicon is one of the most important materials in the modern world. It’s used in everything from computer chips to solar panels. But where does silicon come from?
The answer is simple: sand. In fact, silicon is the second most abundant element in the Earth’s crust, second only to oxygen. So it’s not surprising that it can be found in large quantities in places like deserts… and all over your clothes after a walk on the beach.
However, the silicon found in sand is impure. It comes in the form of silicon dioxide or, as it’s better known, quartz. So, how do they extract pure silicon? Put another way, how is silicon made from sand?
Chemical Vapour Deposition
To turn sand into silicon, it first needs to be purified. The sand is melted with coal, coke or another carbon-rich material. This process, known as chemical vapour deposition, takes place in a large arc furnace at a temperature of around 2000 degrees centigrade for up to eight hours. This causes a chemical reaction whereby carbon in the coal removes the two oxygen atoms from the silicon dioxide. The result? Molten, metallurgical-grade silicon.
Oxidisation
The liquid metal is treated with oxygen to reduce the amount of aluminium impurities. The silicon produced will have a purity of somewhere between 98.5% and 99.9% with miniscule traces of iron, aluminium and calcium.
Cooling and Processing
This is then poured into large cast iron moulds and allowed to cool to a solid, after which it may be used for many different applications. It might be cut into wafers to create computer chips. Or it can be finely powdered with giant needle-like structures, known as cone crushers, and used to make silicone. So, how is silicone manufactured from this powder?
How is Silicone Produced from Silicon?
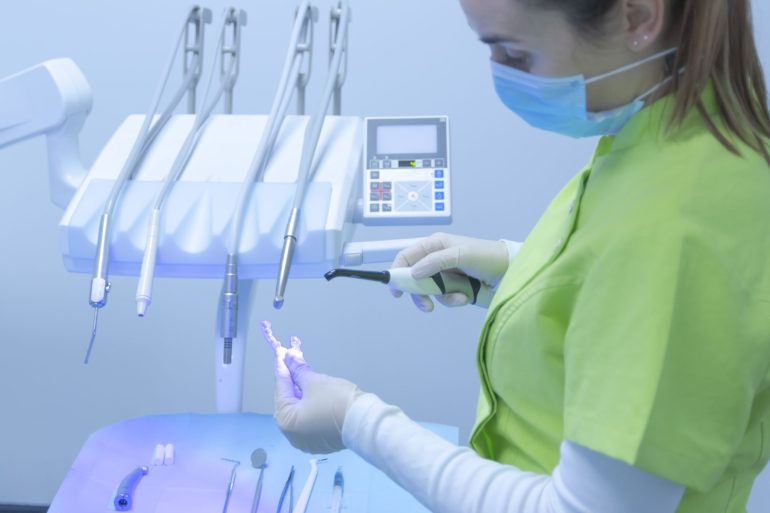
Dentist using polymerization lamp in dental clinic ( Photo: Cavan Images via Getty Images)
In terms of how silicone is made from silicon, this requires a series of chemical reactions. The majority of these entail mixing components at extremely high temperatures or distilling them. Each successive step creates a different compound, each one closer to the desired end product: silicone. It can be broken down as follows:
Making Methyl Chlorosilane
First, the silicon powder is mixed with methyl chloride. In practice, this is carried out in a machine known as a fluidized bed reactor. This is essentially a large tank with pipes running to and from it. Within the reactor, the methyl chloride is passed through the silicon powder at high velocity, under slight pressure and at a temperature of around 300 degrees centigrade. This creates the chemical compound methyl chlorosilane, which contains both chlorine and silicon atoms.
Separating Chlorosilanes
Methyl chlorosilane contains a variety of different compounds, each of which can be used to make different types of silicone. Each of these has different boiling points, so they can be separated through distillation, applying different precise temperatures depending on which one is to be extracted.
Making Silicone: Polymerization
The next steps depend on the type of silicone intended to be created. Different chlorosilanes react differently to processes such as hydrolysis and condensation. Thus, one will produce silicone fluid that can be used in cosmetics. Others will create grease, oil, rubber or resin. This is the final step in the process of how silicone is made.