You may be surprised to know that the origins of golf can be linked to similar games stretching back thousands of years.
The ancient Romans played a game known as paganica, where they used a curved stick to hit a leather ball stuffed with feathers, while between the eighth and fourteenth centuries AD, the Chinese played ‘chuiwan’ (chiu translates as ‘to hit’ and wan means ‘small ball’). The French, Persians and Dutch all played similar games of varying varieties and differing styles and popularity, with some of the details lost to history.
One fact we do know regarding the origins of golf is that the modern game itself originated in Scotland in the fifteenth century.
The History of the Golf Ball
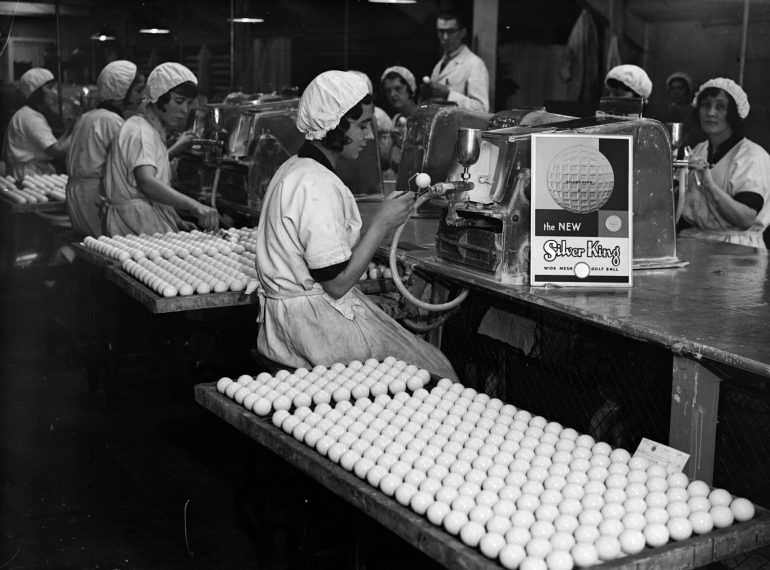
27th December 1932: Workers manufacturing golf balls at the Silver King factory. (Photo: Fox Photos via Getty Images)
So how were golf balls made in the past? The first golf balls were actually made of wood, fashioned from boxwood or beech trees. Another early incarnation of the golf ball was known as a ‘feathery’ ball. This was a ball made up of small leather panels stitched together and filled with boiled feathers, usually goose. However, these historic golf balls weren’t very practical. They were expensive to make, they often split on impact and became waterlogged.
Through the next four hundred years, the humble golf ball went through many iterations and today, the top manufacturers compete hard for market share. Today, the modern golf ball looks very different to its historic counterpart, and the process of how are golf balls are manufactured is a precise and detailed operation.
From Rubber Core to The Ryder Cup - How are Golf Balls Made
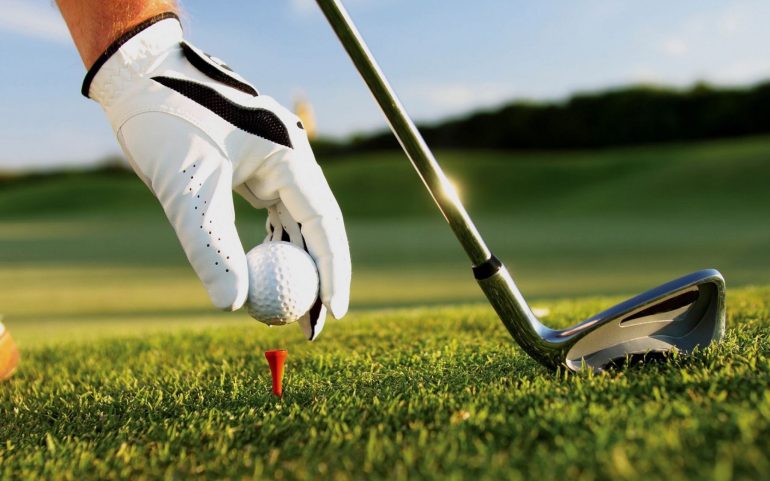
Tee-Off (Photo: Rohan Gohil / EyeEm via Getty Images)
As with all specialist sporting equipment – such as tennis rackets, bowling balls or footballs – the exact manufacturing processes of the big brands are closely guarded secrets. However, generally speaking, the process of manufacturing golf balls will follow the same basic approach, regardless of manufacturer.
Appendix III of the Rules of Golf – governed jointly by the United States Golf Association and the Royal & Ancient – state that the diameter of a golf ball can’t be smaller than 42.67mm, and they may not be heavier than 45.93g. The dimples must be symmetrical, but there’s no limit to the amount of dimples on a ball. With the rules defining the key factors required by a golf ball, the manufacturing process itself is usually broken down into a number of key stages:
The Core
This is the first step on the way to understanding how golf balls are made. Rubber is mixed with other chemicals to create a liquid in the consistency of thick pancake batter. It is then rolled out like a pie crust and cooled between two steel rollers. These rubber sheets are rolled up, and the condensed rubber is pushed through a machine. Out the other side come pellets that resemble big marshmallows called ‘slugs’. These rubber slugs are placed into perfectly spherical steel moulds and are subjected to over a tonne of pressure. At the same time the slugs are hardened at around 170°C for 10-15 minutes. After this hardening process, the slugs are water-cooled, while any excess rubber is returned to the start of the process for recycling.
The Outer Shell
The next step in the process of how golf balls are manufactured is the formation of the outer shell. Once the cores have been cooled, they are transported to another mould and then compression-moulded simultaneously from the top and the bottom with molten thermoplastic – usually urethane – to form the outer coating of the ball, including the dimples. Heat and pressure applied at this stage cause the two halves to fuse together.
The Perfect Finish
At the join, there is a very thin line of excess material which is smoothed away, and then the balls are sprayed with two even layers of white paint. The balls are stamped with the manufacturer’s logo and if required, a model number. Finally, a clear layer of polyurethane is applied to add shine to the ball as well as providing resistance to scuffs, chips and any damage that can affect the flight of the ball or a perfect contact with the club head.
Quality Control
Like baseballs, golf balls are quality controlled using what’s known as a Coefficient of Restitution. This is used to measure the ratio of initial speed to return speed, after the ball has been fired against a metal plate. In addition some manufacturers will test the balls in wind tunnels for lift and resistance, and offer performance data including velocity, rate of spin, distance and accuracy. All this information is useful for the manufacturer to improve their production methods as well as within their marketing materials. If a manufacturer can say their balls go further, faster and with more accuracy than the other guys, they’ll sell more.
Driving through History
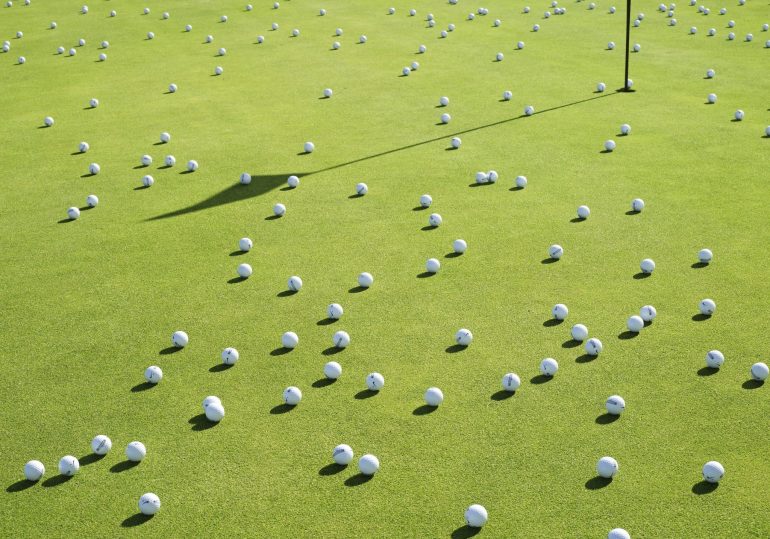
Multiple golf balls sitting on the green near the flag and hole (Photo: Michael Blann via Getty Images)
From the initial wooden golf balls, to feather-filled leather and on to today’s carefully-manufactured products, the story of the humble golf-ball is one that has evolved over centuries. And with golf ball production processes continuing to change with new technology, the story of how a golf ball is made may not necessarily be over quite yet.